IAR 80
Jump to navigation
Jump to search
This article has been nominated for deletion since 23 February 2013. To discuss it, please visit the talk page.
Do not remove this tag until the discussion is closed. Reason for the nomination: Development ended, developer removed this aircraft from FlightGear. |
![]() IAR80 in the default Romanian livery. | |
Type | Fighter aircraft |
---|---|
Author(s) | Emilian Huminiuc |
FDM | YASim |
--aircraft= | IAR80 |
Status | Advanced production |
FDM |
![]() |
Systems |
![]() |
Cockpit |
![]() |
Model |
![]() |
Download |
![]() |
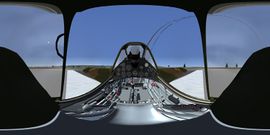
A full spherical panorama of the IAR 80 3d cockpit
The IAR 80 was a Romanian World War II low-wing, monoplane, all-metal construction fighter aircraft. When it first flew, in 1939, it was competitive with most contemporary designs like the German Bf 109E, the British Hawker Hurricane and the Supermarine Spitfire.
Aircraft Features
Livery System
- Besides the default livery there are two additional ones, a bare-metal one and another fictional one in the current Romanian Air Club scheme.
- Changing livery also changes the reflectivity of the material, thus the default one is rather matte, while the two others have increased reflectivity. Livery textures are .dds, improving loading time when switching liveries.
Shader Effects
- The IAR-80 uses the ubershader shader, giving it increased detail. Normalmap texture is also .dds, which improves the apearance of the relief effects. It uses the new dynamic dirt/grit feature implemented in the shader to add oil staining to the fuselage as engine wear increases.
Particle Effects
- Engine smoke, changing colour and density with the thrust and mixture.
- When the engine experiences increased wear, there's also darker denser smoke.
- Particle contrails.
- Wingtip vortices when near stall AOA.
- Propwash when on ground/at low altitude.
View Effects
- By use of Nasal, the internal view shakes when rolling on the runway, and to simulate the buffeting experienced when aproaching stall AOA.
Controls Filter
- Also via a Nasal script, the control input is filtered resulting in decreased input to the control surfaces due to the airflow over them, also this was necessary as the elevator had dynamic compensator tabs.
Submodel Bullets
- No warbird is an warbird without it's claws. Thus submodel bullets are implemented, with particle smoke and sounds too.
- Recoil is simulated too.
Advanced Engine Startup and Management
- The startup procedure is rather 'realistic', from a dark and cold state. While flying you have to take care of the engine (see the help section below).
Engine Sputter
- The engine sputters when overheated/worn due to incorrect management.
- The engine sputters when low on fuel.
Aircraft help
Specific Key Bindings
- ctrl+d: open/close the canopy.
- r/shift+r : open/close the cowling flaps.
- e : fire guns
- Throttle direction is reversed (similar to helicopter controls)
- All other keybindings are the default ones.
Cockpit Reference
- You'll find a quick-reference pdf file in the IAR80/doc folder.
- When pressing ctrl+c to show hotspots, you will also get labels on all instruments, switches and levers that are active.
Clickable Levers and Sliders
- All the levers and sliders in the cockpit are clickable, and use LMB to increase value/position and MMB to decrease the value/position.
Alternately you can use the scroll wheel to make finer adjustments.
Startup
- Turn master switch on (the big hexagonal button over the pilot's right shoulder).
- Set mixture to rich (lever at forward position).
- Set some throttle.
- Prime 6-9 times.
- Set prop-pitch to middle position.
- Set magnetos to M1+2.
- Open the cowl-flaps ("r" key).
- Engage starter button and hope it will start.
- Optional: if wanted you can turn the position lights on.
- If the engine doesn't start, just sputters, it usually means you have not primed enough. To check if that is the case, keep an eye on the fuel-pressure gauge (on the left pannel, the gauge with two needles on it, the right needle), it should increase when you engage the starter. Also, when priming, make sure the lever reaches the forward end of travel, otherwise that push doesn't register.
Warm-up
- Set prop-pitch for minimum revs (towards the rear)
- Add some throttle until boost pressure reaches ~400 (engine rpm will stabilise at about 1250-1300)
- Wait until oil pressure gets over 1 and oil-temp reaches 60
Taxi
- Set prop pitch towards half.
- Adjust the seat position to a higher setting, for better visibility.
- Use the differential brakes to steer the plane.
Takeoff
- Close canopy if you have not done so yet.
- Set flaps to position 2 (30 degrees). (optional, on short runways)
- Set prop-pitch to full.
- Set throttle to have about 950 boost pressure.
- Release brakes and be prepared to correct the aircraft's tendency to yaw to the right (either by braking (at low speeds) or by using opposite rudder).
- Maintain a little back pressure on the stick until the tail lifts off the ground.
- Maintain little back pressure (just enough to keep the plane level) until about 150-160 km/h when the plane should take off.
- Raise gear.
- Raise flaps at about 200km/h.
Cruise
- Set prop pitch so that the needles of the indicator form a V around the 11:05 position.
- Set mixture lever at about the apex of the bend in the lever guard. (~0.6 - 0.7 mixture).
- Cowl flaps at position 4/8.
Landing
- Reduce throttle.
- Open the cowl flaps.
- At about 300 km/h start extending full flaps.
- At about 250 km/h extend gear.
- Touchdown at ~150 km/h.
Emergency
- If you lose the engine during flight the hydraulic system loses presurisation making it inoperable.
- Although flaps and brakes become inoperable there is an emergency landing gear deployment procedure that you can use:
- set the gear safety knob to the safe position.
- check the air pressure gauge.
- there needs to be enough air pressure for gear deployment (>70).
- if air pressure is too low, pump using the manual pump on the right of the cockpit.
- check airspeed below 250 kph.
- release the gear emergency lever on your left side.
- check gear down and locked as indicated by the gear indicator.
Limits
- Maximum flap extension airspeed - 300 kph. (if exceded flaps jam, can be reset by the failure manager)
- Maximum gear extension airspeed - 250 kph. (if exceded gear will jam, can be reset by the failure manager)
- Vne 750 kph IAS. (if exceded aileron/elevator/rudder will tear off, depending on their position, can be reset by the failure manager)
- Maximum g-load - 7G. (if exceded the wing will bend, resulting in bad aerodynamic behaviour, can be reset by the IAR80 menu)
- Maximum negative g-load - 4G. (if exceded same as #4 above)
Engine Management Precautions
- The engine will exhibit increased wear signs and will eventualy stop if you do not follow these guidelines:
- Do not exceed 950 boost (except ocasionally on take-off / in emergency).
- Keep below 1500 rpm until engine warm-up complete.
- Keep below 2800 rpm in normal flight.
- Keep the oil temperature below 120 degrees C.
Gunnery Controls
- By default the weapons are not armed. If you desire you might set their corresponding switches to your pleasure.